Carbon fiber is a high-performance material that is increasingly used in a wide range of applications, from aerospace to automotive and sports equipment. This lightweight and strong material is made by weaving together strands of carbon atoms to create a fabric that can be molded into various shapes and forms.
In this article, we will take a closer look at how carbon fiber is produced, and the techniques used by manufacturers to create high-performance materials.
Raw Materials for Carbon Fiber Production
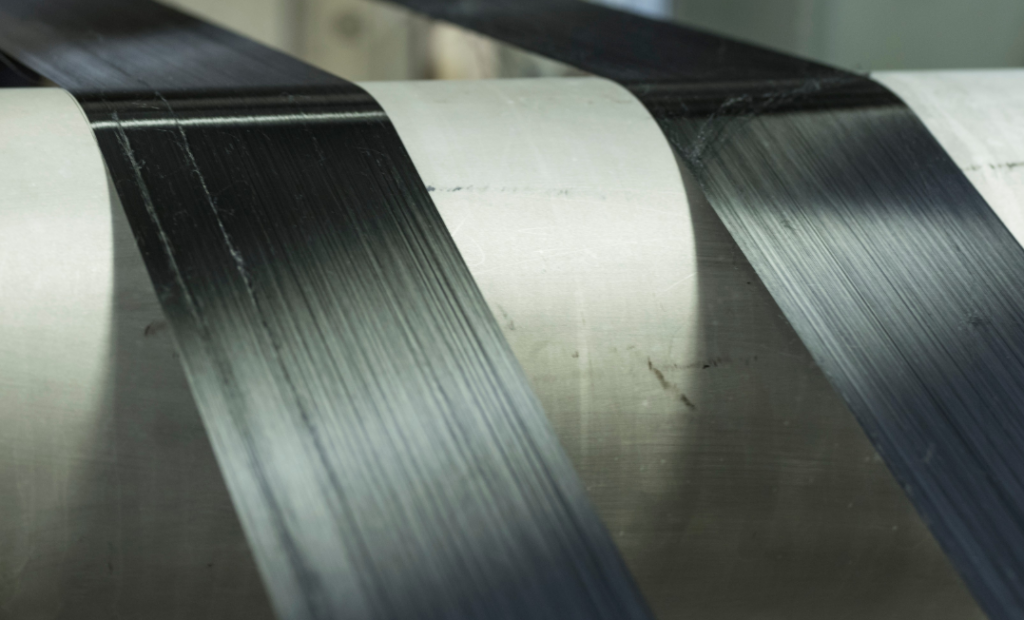
Source: compositesworld.com
The primary raw material used in carbon fiber production is polyacrylonitrile (PAN). PAN is a synthetic polymer that is derived from petrochemicals, and it is the most commonly used precursor material for carbon fiber production. Other precursor materials used in carbon fiber production include rayon, pitch, and lignin.
Carbonization Process
The carbonization process is the key step in the production of carbon fiber. During this process, the precursor material is heated to high temperatures, which causes the atoms in the material to align and form long chains of carbon. This process results in the creation of a carbon fiber bundle, which consists of thousands of individual carbon filaments.
The carbonization process can be carried out using different techniques, including batch and continuous processing. In batch processing, the precursor material is heated in an oven or furnace in batches, while in continuous processing, the precursor material is fed through a series of furnaces in a continuous process.
Surface Treatment
After the carbonization process, the surface of the carbon fiber bundle is treated to enhance its properties. The surface of the carbon fiber bundle is usually rough and uneven, which can impact its performance in certain applications.
To overcome this, the surface of the carbon fiber bundle is treated with a sizing material. The sizing material is a type of resin that is applied to the surface of the carbon fiber bundle to improve its handling and mechanical properties.
Molding and Shaping

Source: youtube.com
Once the carbon fiber bundle has been treated, it is ready for molding and shaping. Manufacturers use a variety of techniques to mold and shape it, including compression molding, resin transfer molding, and vacuum bagging.
Compression molding involves placing it in a mold and applying heat and pressure to shape it into the desired form. Resin transfer molding involves injecting resin into the mold, while vacuum bagging involves applying a vacuum to the mold to remove any air and ensure that it adheres to the mold.
Testing and Quality Control
After it has been molded and shaped, it is subjected to rigorous testing and quality control measures to ensure that it meets the required specifications.
Carbon Fibre Manufacturers UK, for example, may use advanced testing equipment to perform a battery of tests, including tensile strength testing, compression testing, and fatigue testing, among others, to verify the mechanical properties and structural integrity of the finished product.
This helps to ensure that carbon fiber products manufactured in the UK meet the highest standards of quality and performance.
Conclusion
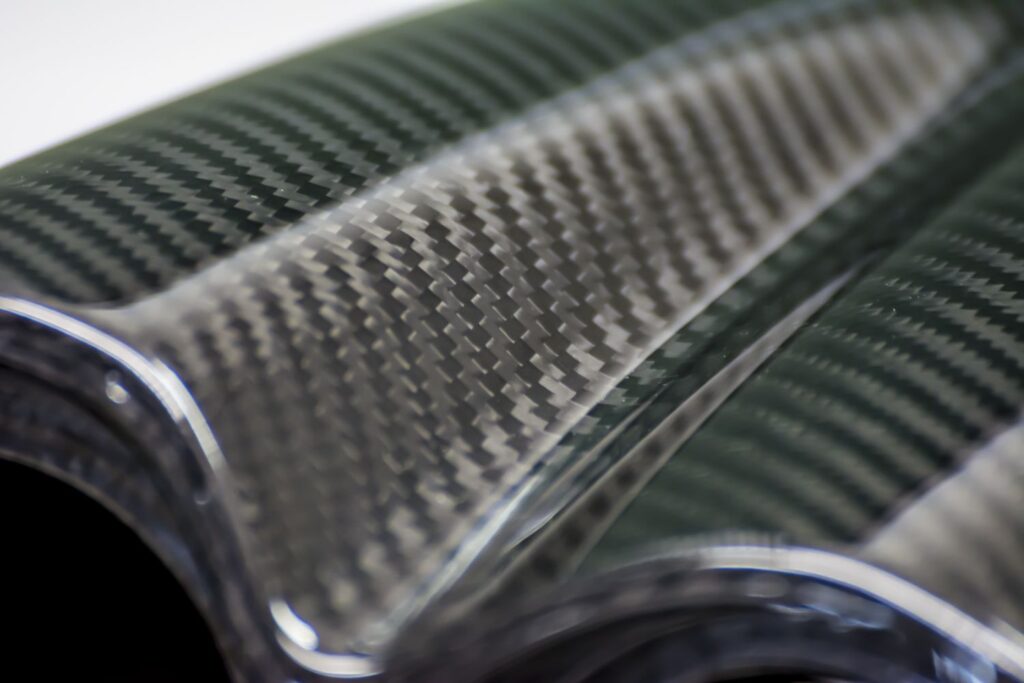
Source: thoughtco.com
Carbon fiber is a high-performance material that is increasingly used in a wide range of applications. The production involves several steps, including the use of precursor materials, carbonization, surface treatment, molding, and shaping.
Manufacturers use a variety of techniques to produce it, and the final product is subjected to rigorous testing and quality control measures to ensure that it meets the required specifications. By understanding the process of production, we can appreciate the unique properties of this material and its potential applications in the future.